圖為清華大學教授李建秋發表主題演講
了解更多內容,請點擊直播專題:中國電動汽車百人會論壇(2018)
在中國電動汽車百人會論壇(2018)的“燃料電池產業化路徑與政策環境”主題論壇上,清華大學教授李建秋發表主題演講。
以下為演講實錄:
尊敬的徐冠華部長、干勇院士、吳志新主任,各位專家,上午好!很高興有這個機會向大家匯報行業發展趨勢和建議。
目前各整車企業在燃料電池發動機和燃料電池轎車的開發方面都已經形成了相關的體系,從圖中可以看到這些發動機的參數。我們認為目前國際上前四位的豐田、本田、奔馳和現代都已經在這里了,商用車方面稍微有點不一樣,我們對比了轎車的發動機和商用車的發動機,可以看到轎車強調的是功率密度,耐久性做到5000小時可以滿足整車的壽命,但商用車方面的耐久性將會達到20000小時,功率密度是比較低的。我們也對全球燃料客車的情況做了對比,客車的發動機基本上除了豐田用的就是MIRAI金屬雙極板發動機,其他幾家用的還是石墨雙極板。
最近兩年國際上在卡車方面也開始了。Nikola-One提出了燃料電池和封閉驅動的重卡牽引車的概念,也推動了國際上燃料電池卡車的研發。日本日野卡車用的是MIRAI的兩套動力系統,豐田也在美國推出了30噸八級卡車,巴拉德也在做類似的卡車,還有其它方面的環衛車,可以看到國際上在燃料電池重型車輛方面已經開始研發了。
去年通用汽車推出了SURUS軍用無人駕駛燃料電池車輛通用底盤平臺的概念,我們認為這個概念也是非常好的??梢钥吹竭@種車是沒有駕駛室和方向盤的,燃料電池、發動機和氫系統都在底盤的下面,是無人控制的。這樣的通用無人平臺既可以作為普通貨物的運輸車,也可以將來在戰場上用來救護,所以用途是很廣泛的。
我們對國際上的這些車輛本身的性能進行了對比,有的數據不一定完全準確,因為我們是通過各種渠道收集來的。我們想給大家一個最深的印象:特斯拉純是純電動的,2噸的車跑400公里;現在燃料電池車可以控制在1.8噸,能跑600-700公里。日產車的數據是五年前的,五年前就停止了燃料電池車的開發沒有跟進,后面的都是最近五年新開發的車。不進則退,最近五年燃料電池車的技術是一年比一年進步。2014年底豐田推出了MIRAI,2016年推出Quality,到現在現代推出NEXO車,駕駛的感覺是一輛比一輛好,這是我們總的印象。
這樣的發展情況下,我們也對全球燃料電池的發展趨勢有了一個根本的判斷。這種判斷更多的是給投資人講的。今天參會的很多人對這個行業還不是很了解,所以我們想在這里和大家做一點宣傳。氫燃料電池大家都不太熟悉,還是需要多宣傳。如果到2020年,按照20萬臺/年的產量,燃料電池系統的成本大概是7000美元,大數就是4萬元人民幣,滿足歐VI排放的傳統發動機也就是這個價格。除了燃料電池還有儲氫、電池、變速箱和驅動系統,加起來動力系統是1.5萬美元,加上1萬美元的附件和其它成本,整車大概是2.6萬美元,也就是15-20萬元人民幣。傳統內燃機B級車的價格,如果讓你買一個3分鐘加滿氫氣就可以跑500公里,天南海北零下幾十度啟動也沒有問題的車,你愿不愿意買呢?我想老百姓還是愿意買的,這就是將來的發展趨勢。
現在鉑的載量還在進一步下降。目前關鍵材料領域是1千瓦不到0.1克鉑,也就是100克的發動機大概不到10克的鉑,全球已經投產的發動機當中,做得最好的是本田的Quality發動機,12.5克鉑的載量,豐田和奔馳的發動機是20克鉑?,F在國內做傳統內燃機排放后處理的企業,它們鉑的用量,如果要做到歐VI的排放也要幾十克鉑。這兩個已經拉平了,這樣的形勢之下燃料電池貴金屬的用量和成本不再是問題。
基于這樣的國際形勢,結合張進華秘書長做的技術路線時候我們判斷下一步的重點是怎樣把產量提升上去,要通過上量做好降低成本。耐久性方面也要有突破,我們預計客車到2020年大概會有5000-10000輛商用車,這是2014年做的判斷,三年以后的2018年我們還是維持這個判斷。2017年我們統計了全國燃料電池商用車接近1000輛,就是幾家合起來,包括大化所和億華通的,未來幾年還是會繼續發展。通過前面1000輛左右的量,產業鏈整合以后,各個環節的成本下降很快。
關于耐久性也有一個材料領域發展的技術路線圖。首先是把膜本身的穩態壽命提高到3萬小時,同時針對車用工況,包括停機、溫度循環、電堆不一致以及膜的機械耐久性,現在可以做到5000-6000小時。下一步到2020年的目標是做到1萬小時,其中主要的工作是在機械膜的破裂、電堆的不一致性和溫度的不循環方面開展。我們努力的方向是到2025年達到2-2.5萬小時的實際工況壽命?,F在預計是可行的,因為對2020年1萬小時的耐久性基本上已經有解決的方案。下一步是到2025年的2.5萬小時。2.5萬小時是什么概念?就是公交車每天17個小時可以跑8年,和整車同壽命,耐久性也不是問題,所以從現在到2025年主要的工作就是降低成本、保證壽命。
我們可以參考一下日本,日本最近發布了燃料技術發展路線圖,里程基本上就是800-1000公里。讓我感到比較驚訝的是,日本在金屬板的轎車電堆功率密度已經做到了3千瓦/升,認為將來可以做到9千瓦/升,也就是說燃料電池在材料和工作過程領域還有很大的潛力。且不說怎樣達到9千瓦/升,我們還沒有看到詳細的報道,至少日本的同行已經把這個目標提出來了?,F在我們大負荷發電的時候,一般燃料電池曲線是小負荷的時候電壓高,大負荷的時候電壓低,額定功率時是0.5-0.6伏之間,效率在0.6伏時不到50%。日本提出通過催化劑和材料的改進,將來在額定的發電電壓可以提到0.85伏,這是很有挑戰的一項工作。我們知道現在怠速電壓是0.9-1伏左右,如果從0.9-1伏要拉到大電流的話,大電流會有壓降和擴散的各種極化下降,但是到2040年下降的幅度很小,大概是0.85伏,要在催化劑和材料技術領域做很多的工作才能做到。圖中這里的萬指的是日元,可以看到也是比較低的。我認為日本在燃料電池方面還是引領全球發展的,2018年到2040年燃料電池還有很大的增長空間。
下面講一講我們國家燃料電池的體系能力建設。以前我們只是講研發比較多,因為以前大企業跟進得少,一般講體系的話都是針對大企業來講的,學?;蛘咝〉难邪l企業很難健全這個體系。最近一兩年我們一汽、上汽和長安這些整車企業,包括重汽和濰柴這些國內主流的行業已經開始動了,這讓我們感到特別欣慰。在這樣的形勢下,2017年已經有接近1000輛的產量,我們行業面臨的是怎樣進行體系化的建設。我們也想請相關的領導和專家在這些方面開展體系化的建設工作,大概是六個方面:
首先是機理分析和過程優化體系,主要是在基礎領域,尤其是在材料和傳熱傳質領域。日本的MIRAI我們已經看到了,現在我們還沒有做到3千瓦/升,金屬雙極板大概是2千瓦/升,石墨雙極板大概是1千瓦/升,將來在材料工作過程當中還是有很多工作可以做的。
其它的是電堆設計和集成制造領域、部件配套和測試評價、整車應用與售后保障、氫能供給和安全運維。李所長講得非常好,氫的安全運維體系是不可或缺的一環,我認為氫能源方面作為可再生能源的儲能系統,我們的認識是相同的。
最后一個體系是行業缺人缺得厲害。現在行業當中相互之間挖人,存量就這么多,要挖的話就是漲工資了,但是這點人是撐不起這個行業的,所以我們在兩年前向北京市科委建議,必須在北京的大學當中有做催化劑材料的立項,通過科委的支持給大學老師幾百萬的項目,讓這些老師能夠把學生帶出來。去年、前年和今年科委都陸續立了一批項目,就是專門支持高校做機理分析和電堆設計。課題不大,也不可能做到產業化,但主要的目標是讓這些高校為行業培養人。現在燃料電池行業太缺人了,所以我們把動力電池和燃料電池結合在一起,起的名字叫做電化學動力人才培養體系。以前汽車系培養的人主要是以發動機、變速箱、傳動、底盤這樣的人為主,但是現在我們搞動力的需要增加電化學這一塊的能力,具體包括催化劑載體、膜和膜電極。
武漢理工大學的潘牧老師是第三方的,我們在這方面也是有基礎的,分區診斷和檢測方面,過程優化非常重要的第一步是模擬計算,就是傳熱傳導行不行。我認為最關鍵的是怎么評價仿真和模擬計算,一定要能夠測到不同地方物質的組分。過去我們花了很大的精力來做檢測平臺,現在可以做到內燃機用高壓傳感器看到里面壓力的曲線一樣,我們可以看到電堆流到不同的地方,加了傳感器以后能夠看到那個地方的氣體組分和溫度。
電堆集成方面也有很多制造方面的問題。怎么提高金屬雙極板和石墨雙極板的制造效率,還有相應發動機的外圍配套?,F在我們國家外圍的配套還很不健全,這既是挑戰也是機遇。我們做了空壓機的調研,以空壓機為例子,國內外有蝸桿式空壓機,還有羅茨式空壓機,這是豐田的MIRAI自己做的,但現在更多用的是高速離心式空壓機,就是8-12萬轉,然后用空氣軸承,電機和壓氣機直接一體化系統。這方面對我們國家現在還是一個挑戰,高速機和離心壓氣機也有人做,但是三個軸承連在一起的還是沒有人做,國際上是有人做的。
動力系統、售后服務和整車方面都不詳細說了,包括運維體系等等。最后我想強調的是,電化學動力學的人才培養體系既涉及到傳統內燃機的流動和傳熱學科,也涉及到動力電池的電化學和材料學科,還涉及到DC/DC變換器,就是電力電子電傳動學科。現在我們是在很認真地考慮清華汽車系動力方向的人才培養怎樣在傳統的燃燒、傳熱、傳質的基礎上把電化學、電力電子的課程納入進來。我們已經在課程和人才培養方面做了實質性的改革,這些就是今天我向大家匯報的。
?。ǜ鶕l言整理,未經本人審閱)

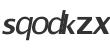