“動力電池產能在快速增加,原材料價格波動較大,尤為明顯的是產線雖然進入智能化的階段,但是電池工廠仍有大量的人員從事著搬運的工作,而隨著勞動力紅利下降,產業也將迎來挑戰?!痹诘谄邔脛恿﹄姵貞脟H峰會(CBIS2022)上,深圳優艾智合機器人(簡稱“優艾智合”)市場部總監關建介紹道。
會上,關建發表了題為《AMR助力鋰電制造物流一體化升級》的主題演講,分析了鋰電池生產制造車間智能化物流發展趨勢和方向,并就行業痛點進行了解析。
關建指出,在鋰電電芯、電極制造布局AGV之前,實際上在3C加工、半導體制造等等很多精密電子制造行業,AGV已經得到了大量的應用。
隨著鋰電池產業的蓬勃發展,產能在快速擴大。關建表示,未來隨著產能擴張,按照現有工廠同比例增加人員數量的話,會對企業用工和成本帶來比較大的壓力,在人口紅利下降的大背景下,這個問題會越來越突出。
據關建介紹,未來如果從AMR(自動移動機器人)的角度,再融合智慧物流軟件系統,“不同種類和類型的機器人形態,共同構成了一套由硬件+軟件集成的完整的自動化物流的解決方案,破解上述產能擴張帶來的人員需求和成本難題?!?/p>
關建表示,不同形態的機器人它們的工作邏輯基本一致,主要是以二維單線的激光雷達作為導引的核心數據來源,通過激光SLAM導航,能夠讓機器人在二維的空間實現正負5毫米誤差范圍進行精確的移動,并實現與生產設備的銜接。
基于底層機器人,會有相應的機器人協作調度系統,多臺機器人可以在工廠車間完成整體調度,“從單體智能通過一步步整合,形成一個相對群體的智能。”關建進一步解釋稱,更重要的是,在機器人這套系統之上,還需要有一套工業物流管理系統——TMS系統,一方面與MES系統打通數據;另一方面與原料倉的WMS系統打通數據,進而實現整個系統的數據鏈接和智能處理。
關建表示,從鋰電生產制造的全局視角看,原料倉包括了噸桶、噸帶、極卷、箔材等生產原料,通過叉車+卡板搬運的是噸桶、噸帶,再以大極卷的形式搬運集中,然后再從涂布到輥壓、分切,一系列的工藝過程中需要用不同形態的機器人完成不同工段的搬運,以及從電芯到模組、PACK段都需要一應俱全的系統解決方案。
在演講中,關建詳細介紹了針對鋰電池生產制造不同工段的產品設計研發思路和應用案例。
資料顯示,優艾智合在半導體行業已經做到了全國工業級移動機器人第一,目前在核心知識產權、出貨量和服務客戶方面都擁有比較驕人的成績,同時產品出口到海外30多個國家和地區,與多家國際企業達成深度合作。業績方面,過去3年的時間里,優艾智合業績年復合增長率約在300%左右。
截至目前,公司在深圳設立了總部基地,并在東莞、蘇州、西安、北京等設有分區域總部或生產基地,機器人月產能達到500臺左右。公司目前團隊成員約500人,其中研發人員占比在50%,參與國家重點研發計劃超過10項,擁有頂層導航系統、機器人調度系統、物流管理系統等自主研發的核心系統,核心知識產權專利超過300項。
客戶方面,與國內外多家電池、半導體等產業頭部企業建立了深度合作關系。

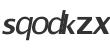